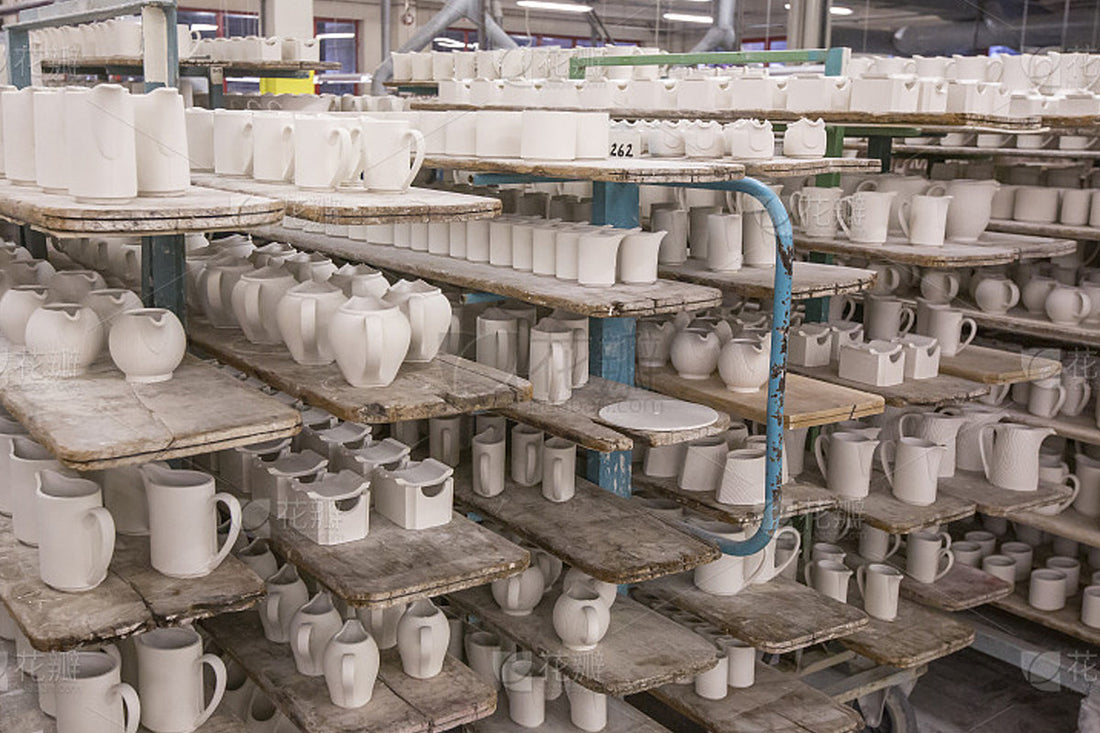
Ceramic Drying Tower Induced Draft Fan Motor Optimization
Share
Industry Background
The ceramic industry is a high-energy-consuming sector in China, with energy use primarily concentrated on electricity and coal gas. Energy expenses account for more than 30% of the total cost of ceramics. Implementing a variety of effective power-saving and rational electricity usage measures to improve energy efficiency, reduce power consumption, and lower production costs has become an urgent priority for enterprises aiming to enhance their economic benefits.
From practical experience in ceramic production, the main driver of energy consumption is the power usage by electric motors. Thus, energy-saving transformations of motors represent the core of energy conservation efforts in the ceramic industry. In China’s ceramic sector, most of the energy is used for firing and drying processes, with the total energy consumption accounting for over 80% of the entire industry’s energy usage. Drying is a major energy-consuming stage in ceramic production, and the energy consumption of spray drying towers alone constitutes 30%–45% of the total. The induced draft fans in ceramic drying towers are mainly used to exhaust moist waste flue gas from ceramic spray-drying towers. Currently, most of these induced fan motors are older-style asynchronous and DC motors. These ordinary high-energy-consuming motors will inevitably be replaced by high-efficiency, energy-saving motors.
Equipment Introduction
Ceramic enterprises can be broadly categorized into building ceramics, sanitary ceramics, household ceramics, decorative/art ceramics, and special ceramics. The following diagram illustrates a typical ceramic production process: raw materials are ground into slurry by a ball mill, then dried into powder by a spray-drying tower. The powder is then formed using a press, glazed and fired in a roller kiln, and finally polished into the finished product. Among these steps, drying is a critical stage in ceramic production: it not only affects product quality but also influences energy consumption and emissions. Therefore, achieving environmentally friendly and energy-efficient drying processes is of great significance for a company’s production and development.
A spray drying tower is a device that can simultaneously perform drying and granulation. Filtered and heated air enters the top air distributor of the dryer, where the hot air is introduced into the drying chamber in a spiral flow. The feed liquid, delivered via a high-speed centrifugal or high-pressure atomizer at the top of the tower, is atomized into extremely fine droplets. These droplets come into contact with the hot air in concurrent flow and can be dried into the final product in a very short time. The product is continuously discharged from the bottom of the drying tower and a cyclone separator, fine dust is collected by a pulse bag filter, and the exhaust gas is expelled by a fan. As shown in the process flow diagram, this method is suitable for the preparation of alumina, tile materials, magnesium oxide, talc, and more in the ceramic industry.
The induced draft fan of a ceramic drying tower is primarily used to remove moist waste flue gas from the ceramic spray-drying tower. By rotating its impeller, the fan generates negative pressure and is typically installed at the kiln’s outlet. The high-pressure draft creates negative pressure in the furnace to ensure complete combustion, expels waste gas, and plays a vital role in the desulfurization and dust removal systems. To a large extent, the induced draft fan determines the operational status of the entire system. Its main components include the fan housing, inlet box, inlet port, drive unit, impeller, bearing box, and regulating damper. It is directly driven by a motor through a metallic diaphragm coupling.
Operating Conditions Overview
Load Characteristics: The fan load exhibits a squared-torque characteristic. Airflow is directly proportional to speed, while pressure is proportional to the square of the speed.
Starting Characteristics: Because of the large inertia, the motor may be freely rotating prior to startup. Therefore, a speed-tracking (or “flying”) start is required—i.e., starting the motor while it is already in motion.
Transported Medium: High-temperature, high-humidity air, with the medium’s temperature up to 200°C (392°F).
Power Configuration: In the existing market, fan sizing and design margins are often generous, leading to low efficiency. A typical power configuration uses a three-phase asynchronous motor plus a variable-frequency drive (VFD). Such motors generally have low energy efficiency and a narrow high-efficiency range, which frequently causes operation in a low-efficiency region and leads to suboptimal overall power utilization.
Hiatran Motor Optimization Solution
Original (Pre-Optimization) Drive Configuration: Y1-355L-4 three-phase asynchronous motor + VFD, 400 kW / 1485 rpm, IE2 efficiency rating
New (Post-Optimization) Drive Configuration: HCM5 magnet-assisted synchronous reluctance motor + HCD-G6 synchronous reluctance drive, 400 kW / 1485 rpm, IE5 efficiency rating
After the upgrade and a 7-day test, the solution achieved an average daily power savings of 384 kWh, yielding an impressive energy savings rate of 18.8%.