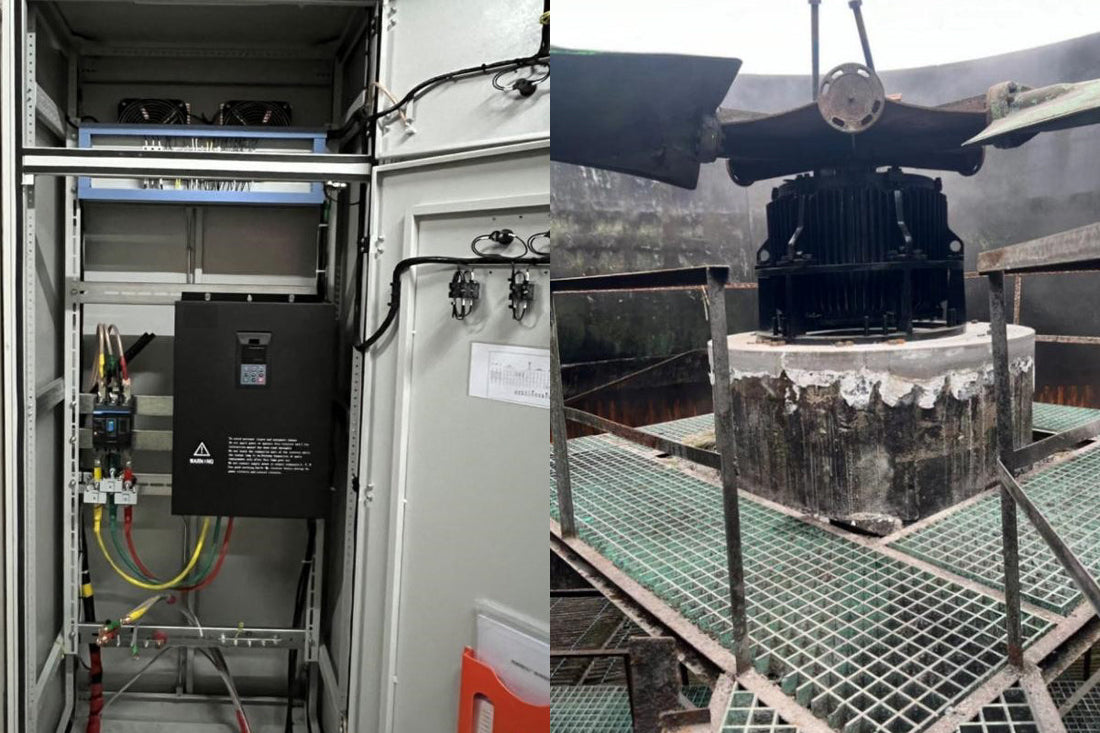
Cooling Tower Motor Transformation
Share
95% of traditional cooling tower motors are asynchronous motors with "reducer + belt drive" to drive the cooling tower fan to achieve the cooling effect of the cooling tower. This combination configuration has the following disadvantages
1. The transmission motor is an asynchronous motor with low working efficiency and high energy consumption;
2. The reducer gear transmission has large vibration, high noise, low efficiency, and high maintenance cost. Belts, gears, and pulleys are wearing parts and require maintenance all year round. Moreover, this configuration is large in size and complex in installation structure, and it is no longer in line with the country's environmental protection and energy conservation and emission reduction policies. Therefore, how to improve the efficiency and power of cooling tower motors is of great significance for the comprehensive implementation of energy conservation and consumption reduction work.
Working Principle Of Cooling Tower
Dry (low enthalpy) air enters the cooling tower from the air inlet after being pumped by the fan; high-temperature water molecules with high saturated steam pressure flow to the air with low pressure, and moist (high enthalpy) water is sprinkled into the tower from the water seeding system. When water droplets come into contact with air, on the one hand, due to direct heat transfer between air and water, and on the other hand, due to the pressure difference between the water vapor surface and the air, evaporation occurs under the action of pressure, taking away the heat in the water, i.e. evaporation heat transfer, thereby achieving the purpose of cooling.
Old Programme For Asynchronous Motors
In the original asynchronous motor + reducer (pulley) transformation plan, the motor is connected to the reducer through the main shaft, driving the gears to rotate, and then driving the fan blades to rotate. The intermediate transmission process has a large loss, which greatly reduces the working efficiency. The motor has a high speed, large vibration, high noise, and large working current. In addition, the reducer has a compact structure design, high heat generation, and weak heat dissipation capacity, resulting in high reducer temperature, short oil seal and lubricating oil life, and frequent maintenance.
HIATRAN Synchronous Reluctance Motor Application
Permanent magnet direct drive motor transformation plan The permanent magnet direct drive motor directly drives the fan blades through the inverter speed regulation, reducing the intermediate transmission link, with a simple and reliable structure, basically maintenance-free. Because it is driven by the inverter, it can be remotely started and adjusted, which is convenient for monitoring the running status of the motor at any time. The permanent magnet direct drive motor adopts low-speed and high-torque direct drive technology and intelligent control technology, with a simplified structure, and has the characteristics of high efficiency and low consumption, high stiffness and fast response, and no need for lubrication. At the same time, permanent magnet synchronous motors generally choose rare earth permanent magnet materials (NdFeB) as permanent magnets. At present, the price of rare earth materials is relatively expensive, and the initial investment cost is high. When the temperature is too high, the rare earth permanent magnet synchronous motor may produce irreversible demagnetization under the armature reaction generated by the impact current, or under severe mechanical vibration, which will reduce the performance of the motor and even make it unusable. Therefore, attention should be paid to the formulation of the motor heat dissipation plan and measures to prevent vibration in the use environment.
HIATRAN low-speed direct-drive magneto-assisted synchronous reluctance motor transformation plan The low-speed direct-drive magneto-assisted synchronous reluctance motor directly drives the fan blades through a vector inverter, without the loss of the intermediate transmission device. Compared with the traditional structure, the power saving rate can generally reach more than 30%, and the motor efficiency can reach 96%. The motor has high torque and low speed, low vibration and noise. The control is remotely started and speed-regulated, which is convenient for monitoring the motor operation status. The magneto-assisted synchronous reluctance motor does not contain rare earth permanent magnet materials. It uses ferrite magnetic materials as auxiliary excitation and reluctance torque as the main torque source. The rotor has no loss, simple structure, stable and reliable, low reactive power, high efficiency, wide high-efficiency range, and good comprehensive operation economy. In addition, ferrite materials are not easy to demagnetize in high temperature environments, which is safer and more reliable than permanent magnet motors. Even after the motor is demagnetized, it can still be used as a pure reluctance motor, but the efficiency will be slightly reduced.
Before transformation: asynchronous YE2-280S-4 75KW-1470+frequency conversion
After transformation: HIATRAN low-speed magnetic-assisted synchronous reluctance direct drive + frequency conversion 75KW-155rpm, The effect after transformation is as follows