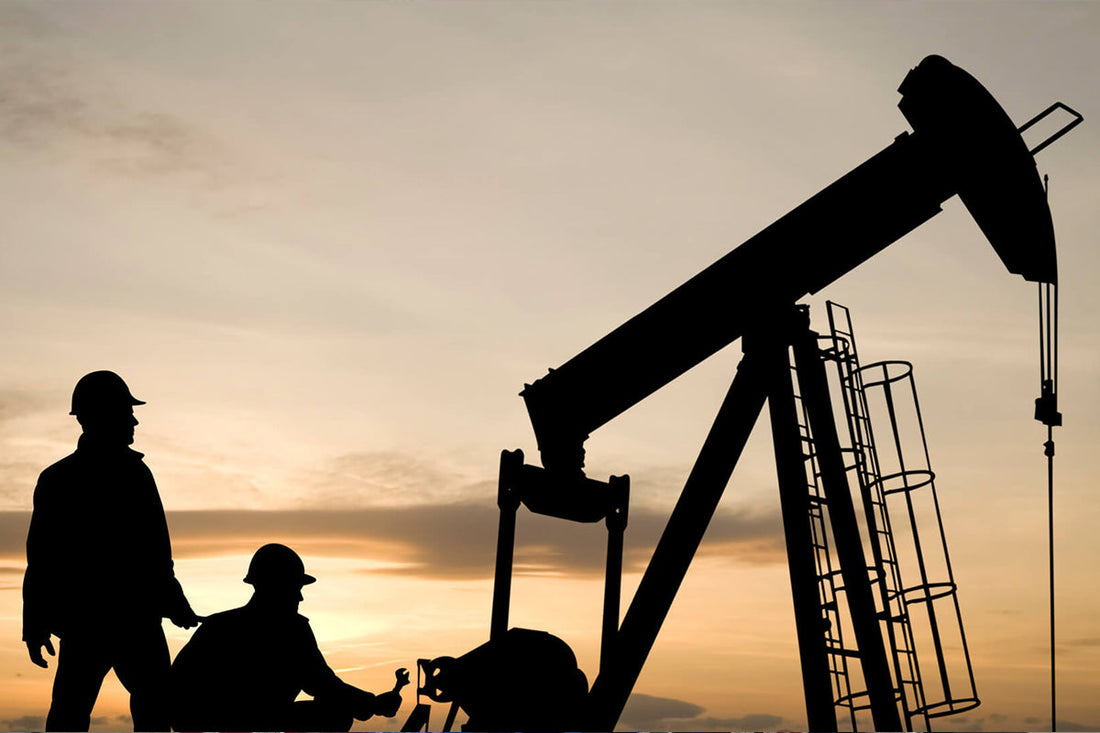
High-Efficiency Transformation of Oil Pump Unit Motor
Share
The pumping unit is one of the most representative oil extraction equipment in the oil field. Its main function is to mechanically extract the crude oil from the well to the ground. The pumping unit is a mechanical oil extraction equipment. Its working principle is based on the "crank-connecting rod mechanism". The motor drives the crank to rotate, which in turn drives the crossbeam to swing up and down, thereby driving the pumping rod downhole to move up and down, and pumping the crude oil in the formation to the ground through the oil pipe.
The extensive use of pumping unit drive motors makes them the largest power-consuming equipment in oil fields. According to statistics, motor equipment accounts for 80% of the total power consumption of oil fields, but a considerable part of them are in a light-load, low-efficiency, high-energy-consuming operation state, resulting in serious waste of electricity. Many oil fields are still using old asynchronous motors (used for 20-30 years), and some motors are backward in manufacturing technology, and their performance is far behind that of new high-efficiency motors. This leads to low motor efficiency and high losses, and energy-saving transformation is urgently needed.
Pain Points of Asynchronous Motor Drive for Oil Pumping Unit
Poor Adaptability to Load Changes
The load of the pumping unit has significant periodic fluctuations. The load seen by the motor changes continuously in one stroke. There are two critical points of the upper and lower strokes, and even negative torque conditions occur. The speed of ordinary three-phase asynchronous motors is basically unchanged under constant power frequency, and they lack the ability to adaptively adjust such dynamic loads.
Large Starting Current and Obvious Start-stop Impact
Ordinary three-phase asynchronous motors will generate huge surge currents and mechanical impacts when they are directly started. This is because the pumping unit often has significant unbalanced torque in a static state, and the motor needs to provide high torque to overcome static resistance and lift the well fluid column. In order to achieve sufficient starting torque, the motor selection has a large power redundancy, but the cost is to generate several times the rated current impact at the moment of starting. Actual measurements show that the current of the asynchronous motor can be as high as 5-7 times the rated value when it is directly started at full voltage. Such a high starting current not only causes an increase in power loss itself, but also impacts the power grid, causing power quality problems such as voltage fluctuations. At the same time, the thermal stress generated by the large current passing through the stator winding will accelerate insulation aging and shorten the life of the motor.
Frequent Maintenance and Limited Lifespan Reliability Issues
Oilfield pumping equipment has extremely high requirements for continuous operation reliability. Ideally, the pumping unit should operate unattended in the field 24 hours a day, 365 days a year. The three-phase asynchronous motor used is exposed to severe cold and heat, wind, sand, rain and snow in the working environment all year round, requiring frequent maintenance, and its service life will be relatively shorter.
Improve System Energy Efficiency at the Source
Transformation Method:
- Replace ordinary asynchronous motors with IE5-level synchronous reluctance motors
- Use high-performance inverters for dynamic energy allocation
Solution Effect:
- Synchronous reluctance motors have no rotor loss (no copper loss, no induction current heating), and their efficiency is usually 3-10 percentage points higher than IE3/IE4 asynchronous motors
- Its partial load efficiency curve is more stable, and it still maintains high efficiency in the actual long-term "light load" operation scenario of the pumping unit
- Working in conjunction with VFD, it can automatically reduce the speed and frequency when empty or at low liquid level, fundamentally reducing ineffective energy consumption
Reduce Starting Current and Mechanical Impact
Renovation Method:
- VFD uses soft start + soft stop
- Optimize the start-stop strategy according to the current and torque curves
Solution Effect:
- The starting current is limited to 1.5~2 times the rated current (compared to 5~7 times of asynchronous motors)
- Greatly reduce the impact on the distribution system and cables
- The start-stop process is smooth, effectively reducing the wear of the reduction box, gears, and connecting rod systems
Reduce Manual Maintenance and Improve System Reliability
Transformation Method:
- The synchronous reluctance motor has a simple structure, no excitation winding, and no slip ring
- It supports remote monitoring and fault diagnosis with intelligent inverter
Solution Effect:
- Almost maintenance-free (no rotor heating components, small bearing load)
- The VFD system can monitor the motor temperature rise, load fluctuation, and current abnormality to realize the "pre-maintenance" mechanism
- Support cloud monitoring or SCADA system to respond quickly to oil well conditions
Hiatran Transformation Plan
This time, IE5 ultra-high efficiency magnetic-assisted synchronous reluctance motor + driver is used to replace the original ordinary three-phase wound asynchronous motor. The motor energy efficiency is increased to IE5 to achieve motor efficiency improvement.
Old plan: YE2 three-phase asynchronous motor, YD-250M-12/6, 22kw
New plan: Motor: HCM5 series ultra-high efficiency magnetic-assisted synchronous reluctance motor, HCM5-250M-22-750-T4-FIRS-B3
Drive: HCD-G6 series synchronous reluctance driver, HCD-G6-T4022G-B, 22kW
Power Saving Rate 24%
After comparative testing, the results are shown in the table above. The average daily power consumption of the oil pump before the transformation was 254kW.h, and the average daily power consumption of the oil pump after the transformation was 193kW.h. The average daily power saving was 61kW.h, and the power saving rate after the transformation was 24%, which was in line with expectations.