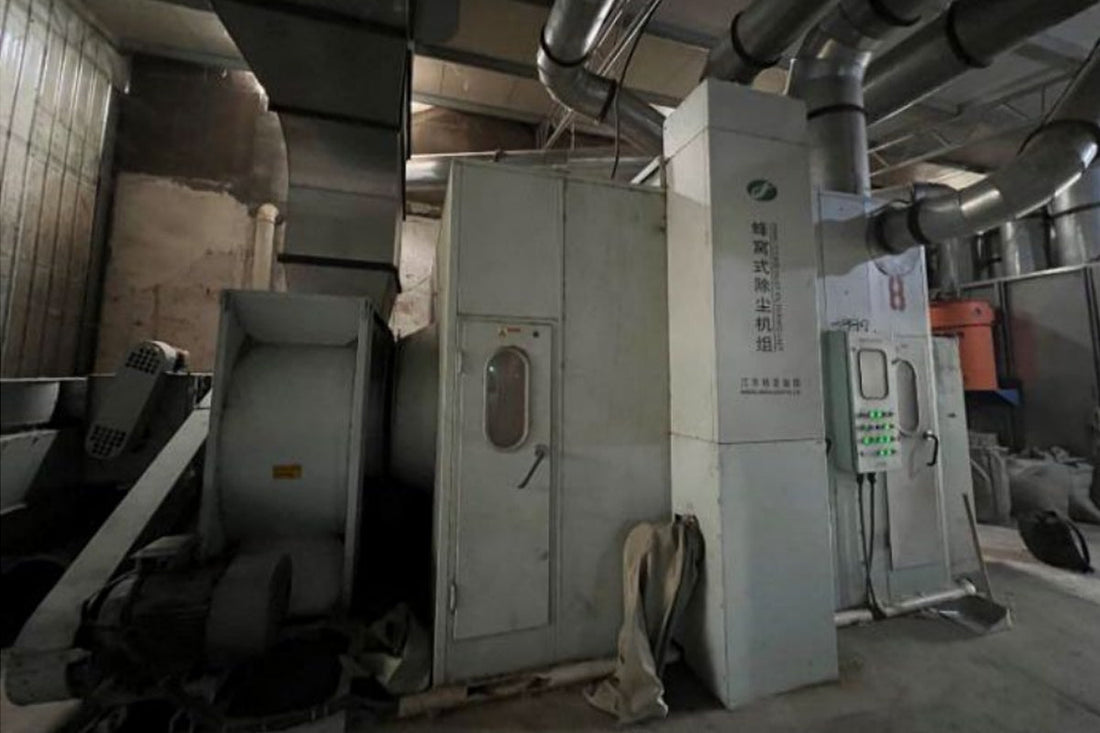
Honeycomb Dust Removal Unit Motor And Driver Optimization Scheme
Share
Honeycomb dust removal unit is an important dust removal equipment in the flax (long hemp) textile industry. The motors configured for the existing honeycomb dust removal unit fans are mostly IE2 energy efficiency, with a narrow overall economic operation range and high energy consumption. Find Hiatranmotor for transformation and upgrading. Improve stability and energy saving effect.
Equipment Introduction: Honeycomb Dust Removal Unit
In the spinning production process of flax (long hemp) mills, according to the process requirements and the requirements for improving the working environment, the following processes generally need to be equipped with process exhaust and dust removal. Manual beam splitting table, combing machine, mixed hemp humidifier, combing machine, slivering machine, drawing machine, needle combing machine, roving machine and other process equipment. The function of the dust removal system equipment is to continuously meet the process production requirements, timely absorb and collect dusty fibers such as debris and dust generated during the production process. To improve product quality, reduce the dust concentration in the workshop, and improve the working environment of workers. The honeycomb dust removal unit consists of two major parts: a honeycomb dust collector and a centrifugal fan.
Working principle of honeycomb dust collector
It consists of the first-stage dust removal unit and the second-stage dust removal unit. The first stage mainly filters, separates and collects fibers and dust in the treated air; the second stage mainly filters, separates and collects particulate dust in the air after the first stage filtration, so that the air is purified to the standard that can be reused or discharged.
Working Condition Introduction
① Load characteristics: fan load, square torque. That is, the air volume is proportional to the speed, the torque or wind pressure is proportional to the square of the speed, and the shaft power is proportional to the cube of the speed. The low-speed load torque is small and the output power is small, and the high-speed load torque is large and the output power is large.
② Operating environment: The room temperature is dusty, and there is a lot of fiber dust in the air. After a long time, these fiber dust will cover the surface of the motor and affect the heat dissipation of the motor.
③ Starting characteristics: direct start, small starting torque; a dust removal unit system is equipped with a centrifugal fan and the dust removal duct is not connected to the ducts of other dust removal systems, so there is no negative pressure start.
④ Power configuration: Common power configurations include three-phase asynchronous motor + inverter solution. The motor has low energy efficiency, narrow high-efficiency range, often runs in low-efficiency area, and has poor comprehensive electricity economy.
Hiatran Electric Solution
This transformation relies on ultra-high-efficiency magnetic-assisted synchronous reluctance motor technology, and takes the honeycomb dust removal unit as the energy-saving transformation object. The HCM5 series ultra-high-efficiency magnetic-assisted synchronous reluctance motor is used as the main drive motor, and the G6 series driver is used as the motor drive control device.
① Motor product introduction
The HCM5 series is a fully enclosed, self-fan air-cooled ultra-high-efficiency three-phase magnetic-assisted synchronous reluctance motor designed and manufactured using new magnetic-assisted synchronous reluctance motor technology. It has the characteristics of high efficiency, large starting torque, low noise and vibration, and wide speed regulation range. The motor does not contain rare earth permanent magnet materials, and the structure is simple, stable and reliable. The standard small and medium-sized asynchronous motor housing is used for easy on-site replacement. It is an efficient motor drive solution that saves energy and rare earth resources. It can be used to drive various general mechanical equipment, such as fans, water pumps, air compressors, textile machinery, etc., to meet the driving needs of various equipment in the field of industrial automation.
② Driver product introduction
The HCD-G6 series variable frequency driver is a general high-performance current vector variable frequency driver that can realize the speed and torque control of the magnetic-assisted synchronous reluctance motor. It adopts high-performance vector control technology, has good dynamic control characteristics and overload capacity, supports full-speed speed tracking start, and is suitable for driving various automated production equipment. It has rich input and output interfaces and supports expansion.
Original drive solution:
YP2-225S-4 three-phase asynchronous motor(37kW-1500rpm) + inverter IE2 energy efficiency
Current drive solution:
HCM5 magnetic-assisted synchronous reluctance motor(37kW-1500rpm) + HCD-G6 synchronous reluctance driver IE5 energy efficiency
After optimization:
After replacement, the actual measured speed of the energy saving rate is 1135rpm on average, which can achieve an energy saving rate of 8.9%.